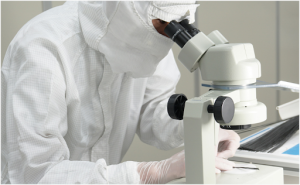

一枚の板から、針が現れた。

「極細の針」は、今まで岡野に持ち込まれた仕事の中でも難題のひとつだった。先細の設計のために、最初は細いパイプの片側を圧縮してみたが、うまくいかない。しかし彼は、平然としている。
「一度やると言ったら、俺はやる」
次に考えた方法は、金型を使った金属プレス。決して新しい技術ではない。だが、今なお最先端のものづくりを支える。携帯電話用のリチウムイオン電池ケースにしても、わずかなスペースに収める都合上、四角く平たい。これをプレス加工で作るのだが、隅の方が切れたり、破れたりしやすい。何度も失敗と工夫を繰り返した末、ついに成功させた。
また、部品をつなぎ合わせることなく一枚の金属板から鈴を作ったこともあった。40年前の技術だが、中が空洞の球体を成形し、開いた口を閉じていく。工程の微妙さは今も、これを真似できる人はなかなかいない。プレスで、できないことはないはずだ。
こうした技術や経験のすべてを注いで考えた。先が細く根元が太い形にするため、薄いステンレス板をプレスし、型を抜き、段階的に曲げ、延ばし、一本ずつメガホンのような筒状にしていく。板の厚みの分、単に丸めたのでは、端と端との合わせ目がパイプの内側でしかくっつかない。この技術で、さらに外側の金属を延ばす。ごく小さく、しかも太さが一定でない形状にもかかわらず、丸めた板の端と端とをぴたりと面で合わせ、閉じるのだ。
いったんできあがったパイプはテルモに持ち帰り、検証にかける。顕微鏡で見ると、はじめは中がつぶれていたり、いびつに歪んでいた。また力の入り具合によっては一カ所だけ薄くなったり、よれてしまうこともあった。
岡野工業とテルモの技術者の間で検証は何度も繰り返された。その度に金型の形状、プレスする力のかけ具合やスピード、潤滑油の配合なども、岡野は長年の経験と感覚で調整し、精度を高めていった。
試行錯誤は1年を超え、作り直した金型は数百個にのぼった。どの断面も完全な円形のパイプが、ついにできあがった。
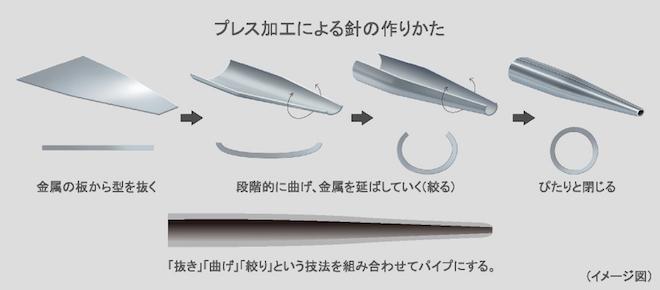
今度は、テルモがこのパイプを針へと仕上げ、医療現場に届ける番だ。医療機器として求められるものづくりの品質を保つ、重要な役目を担う。
開発チームは、さらに痛みを小さくする方法はないか探った。針の先端は通常、左右対称に刃が付けられているが、肌に対してほとんど垂直に刺すインスリン注射では、左右の刃の角度を変えた方がスムーズに針が入るのではないか。針が皮膚を「突き刺す」のではなく「小さく切る」という発想だ。細部に至るまで、工夫できることはないか追求し続けた。
工場での、そうした針先の加工や組み立て。どの工程にも、まったく新しい手法が必要だ。溶接ひとつとっても、これまでの方法では針そのものが溶けてしまう。すべてが挑戦の連続であり、社員が一丸となって取り組んだ。
開発に着手してから5年。ついにテルモの技術者の決意が実を結ぶ時が来た。