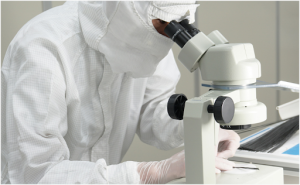

「やってやろうじゃないか」町工場の心意気に出会った。
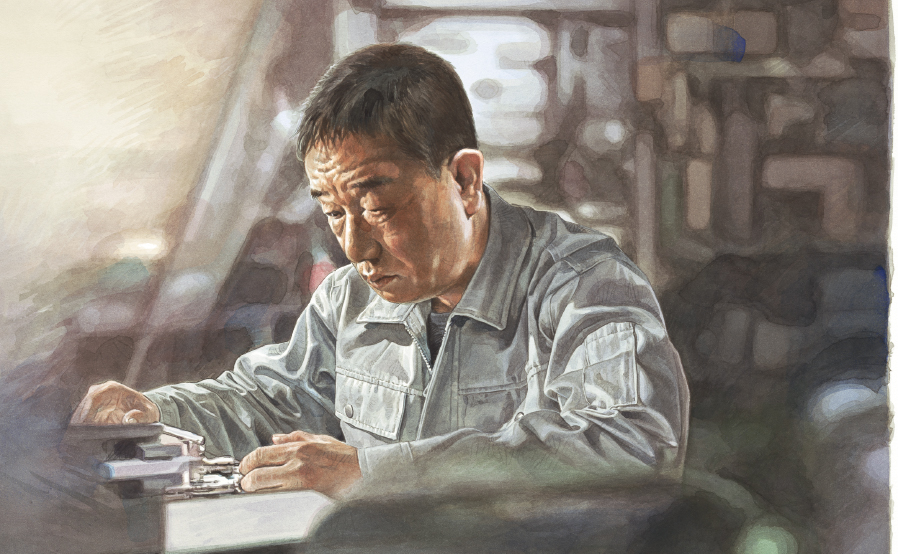
根元が太くて先端が細い、独特な形を描く極細の針。その設計は決まった。だが、大量生産を前提とした製造方法をどのように確立できるか。このときは、アイデアすら見えていなかった。
一般的な針の製法は、こうだ。最初にステンレスの薄い板を丸めながら筒状にし、合わせ目を溶接する。そのパイプを次々と引き伸ばし、目的の細さにする。針の長さにカットしたら、最後にまとめて針先を研磨する。
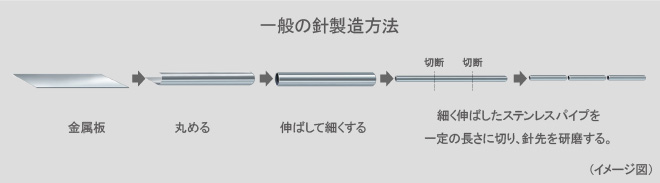
この従来の製法をベースに、パイプを細い穴に通して途中まで引っ張ったり、パイプを外側から叩くなどして先細の形に加工してみた。それでもある程度は作れるのだが、世界中の患者さんに使ってもらうのだから、億の単位で安定して作り、届けられなければ意味がない。
社内開発の一方で、設計を現実の形にしてくれる協力先を探すことにした。大きなメーカーから町工場まで、多くの会社を訪ね説明し続けた。はじめは精密パイプを加工する会社から回り始めたのだが、設計図を見せても、大量生産が可能な技術を提供できると言ってくれるところは現れず、探索をパイプ加工から金属プレス、金型製作へと広げていった。断られ続けても、諦めようという気は起こらなかった。
訪問先が100社を超えたかという頃、東京・墨田区にある従業員6人※の町工場、岡野工業のうわさを聞いた。金属のプレス加工技術で名高いという。
プレス加工は、金属板から立体を作ることができ、大量生産との相性もいい。一枚の平板に金型をあて、段階的に力をかけていくことで、立体的な深い箱型や筒状などに加工していく方法だ。
携帯電話の開発の鍵となった電池ケースも、岡野工業の「絞り」という技術を駆使した高度なプレス加工が実現した。薄く深みのあるリチウムイオン電池の本体そのものを一枚の金属板で一体成形し、それまで発生していた液漏れの課題を解決したのだ。
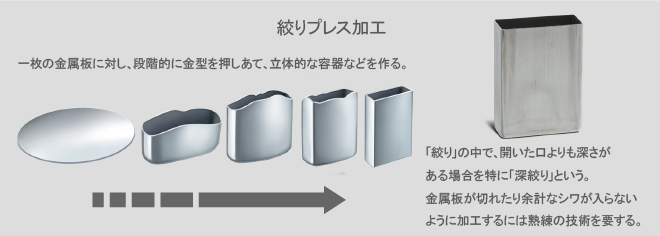
「プレス加工で形にできるかもしれない」
テルモの技術者は、期待を胸にこの町工場を訪れた。
岡野は、はじめは「針はパイプ屋の仕事。金型屋の出る幕じゃない」と断った。しかしこの極細の針は、どこの会社からも「できない」「無理だ」と断られてきた代物だと聞いて目の色が変わった。人ができないことに挑戦するのをモットーとする彼は、「やってやろうじゃないか」と大きくうなずいた。
長年の経験で研ぎ澄まされた読みと勘。そして未踏の領域にひかれる職人魂が騒いだに違いない。
昭和ひとけた生まれの江戸っ子、めっぽう活きがいい。
※
2005年時点